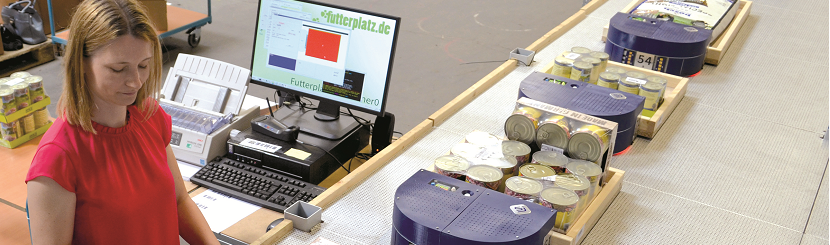
Mehr Lagerfläche, schnellere Lieferung und weniger Fehler bei konstantem Wachstum im E-Commerce
Beschleunigte Kommissionierung und damit verbunden ein dynamisches Wachstum – das ermöglicht das neue automatisierte mehrstöckige Flächenregal STOROJET. Eine für den mittelständischen Versandhändler passgenau entwickelte Ideallösung, die sich auch in puncto Investition rechnet! Hier dargestellt am Beispiel Futterplatz.de.
Hintergrund / Ausgangssituation
Futterplatz.de, seit über 13 Jahren etablierter Versandhändler für Tiernahrung und Zubehör, kann auf ein kontinuierliches Wachstums zurückblicken. Die bestehende Lagerfläche von 1.000 qm erwies sich Ende 2011 jedoch immer deutlicher als zu klein für die mittlerweile rund 8.000 Artikel bzw. 400.000 Einzelobjekte. Da ein weiterer Ausbau am alten Standort nicht möglich war, erfolgte ein Umzug in ein Lager mit 5.000qm Grundfläche. Bald musste die Unternehmensführung mit Betriebsleiter Julius Schmidt allerdings erkennen, dass man hier trotz oder gerade durch die Vergrößerung an Effizienz verlor, auch oder eben weil die Höhe der Halle, bis auf einen kleinen Teilbereich mit Hochregallager, mit ihren 6 m völlig vernachlässigt wurde.
Zwar optimierte man Laufwege und Nähe zu den Kommissionierplätzen nach schnell oder langsam drehenden Produkten, aber mit Regalen von einer Griffhöhe von 1,70m sowie Palettenstellplätzen wurde nur in die Fläche gebaut. Dadurch entstanden zu lange Wegstrecken für die Mitarbeiter, die zudem zu große Lasten befördern mussten. Die Pickzeiten stiegen unverhältnismäßig an. Auch der Einlagerungsprozess nahm unnötig viel Zeit in Anspruch durch das händische Einlagern nach der Entpalletierung und der Definition eines genau passenden Lagerorts. Bei der Lösungssuche wurden verschiedene bestehende Lager- und Kommissioniertechnologien bewertet, doch keine konnte wirklich überzeugen: Zu groß in Auslegung und Investitionsbedarf, nicht flexibel und nicht sukzessive ausbaubar, zu hohe Lern-Anforderungen an die Belegschaft, Stillstand des Tagesgeschäfts während Aufbau und Umzug.
Lagern und Kommissionieren neu gedacht
Da am Markt vorhandene Technologien nicht passten oder investitionsmäßig nicht darstellbar waren, galt es „Lagern und Kommissionieren“ neu zu denken! Hier zahlte sich die langjährige Partnerschaft mit den Schwesterfirmen ICO und Telejet aus. Denn das IT-Know- How von ICO und die Ideenstärke von Telejet mündeten in eine völlig neuartige Lagerautomatisierung. Das Regal blieb als optimale Basis für das Lagern sehr heterogener Produkte, die sich in Größe, Form, Ausprägung, Haptik und weiteren Parametern unterscheiden, bestehen.
Eine neue maßgeschneiderte Lösung
Ausgehend von der obigen Charakterisierung haben Telejet und ICO einen grundlegend neuen Ansatz entwickelt, der auf einem Kern fußt: frei fahrende Roboter, die sich an Codierungen auf dem Boden orientieren. Grob gesagt lassen sich auf den genormten Bodenplatten im definierten Rasterformat Lagerflächen und Wegstrecken bauen.
Detaillierter bedeutet das, dass in einem Regalsystem mit übereinander montierten Ebenen viele Warenträger eng abgestellt und mit kompakten Lagerrobotern verfahren, an- und abgekoppelt werden. Je nach den zu lagernden Produkten können die Warenträger mit individuellen Fächern ausgestattet und unterteilt sein.
Die verschiedenen Ebenen des flexiblen Regalsystems sind durch mehrere Aufzüge miteinander verbunden und ermöglichen den Robotern neben der horizontalen auch eine vertikale Mobilität. Die Roboter sind nicht schienengebunden und können frei fahren, dabei orientieren sie sich anhand der Codierungen auf den speziell beschichteten Böden und werden vom Zentralsystem per Funk orchestriert. Die Lagerroboter haben die Größe eines Mähroboters für den Hausgebrauch, verfügen jedoch über weit mehr Leistung und vollbringen eine beachtliche Transportleistung.
Ein besonderes Merkmal ist die optimale Ausnutzung der Höhe bestehender Lagerhallen zwischen 1,8 und 10 m. Die einzelnen Regalflächen des in sich geschlossenen Systems haben eine Grundfläche von 1,2 x 1,6 m und sind mittels Stahlsäulen miteinander verbunden. Per Software wird definiert, welche Bereiche als Wegstrecke und welche als Abstellflächen gelten.
Probe aufs Exempel
Die Idee, dass auf Basis der definierten Grundflächen Lagersysteme realisiert werden, die sich den räumlichen Gegebenheiten anpassen, konnte sich bei Futterplatz.de gleich bewähren. Zwischen den Tragsäulen der Halle befindet sich der STOROJET-Lagerbereich, während die Verfahrwege zu den Kommissionierstellen außen um die Säulen herum führen. Ein Kommissionierplatz, der vornehmlich für die Einlagerung genutzt wird, liegt in der Nähe eines Hallentores, ein weiterer in der Nähe der bisherigen Packstraße. Für saisonale Peaks wurde zusätzlich ein dritter Arbeitsplatz eingerichtet, um bei Bedarf den nötigen Output zu gewährleisten.
Der Lagerbereich reicht bis unter die Deckenträger, hat eine Gesamthöhe von ca. 5,2 Meter und stellt so auf 400qm Grundfläche 5.000qm Lager- und Verfahrfläche zur Verfügung.
Zudem wurde ermittelt, welche Produkte sich sowohl von Größe und Gewicht her als auch vom Abrufvolumen für eine Einlagerung in das System eignen. Der benötigte Umfang des Lagersystems wurde so gewählt, dass für ein sukzessives Wachstum weitere Ebenen zur Verfügung stehen.
Gerade diese Flexibilität macht STOROJET für mittelständische Unternehmen so interessant. Der Lagerturm kann aus Kostengründen beispielsweise in der Höhe erst halb aufgebaut und dann nach und nach mit weiteren Speicherebenen ausgestattet werden. Auch eine Erweiterung in die Grundfläche ist problemlos währen des laufenden Betriebs durchführbar. Die täglichen Abläufe müssen nicht unterbrochen werden.
Das war auch bei Futterplatz.de der Fall: Aufbau und Erstinbetriebnahme liefen parallel zum bisherigen Betrieb; es gab keinen Stillstand und klassischen Umzug! Ähnlich eines Soft-Openings wird das neue Lagersystem kontinuierlich mit Waren befüllt und Stück für Stück mit mehr Robotern ausgestattet, die die Warenträger bewegen.
Dem jeweiligen Warenwirtschaftsprogramm des Anwenders kann mitgeteilt werden, ob Waren im klassischen oder im automatisierten STOROJET-Bereich zu finden und zu kommissionieren sind. Parallel können die Mitarbeiter im Aufbau- und Befüllungszeitraum das Wissen um die neue Technologie und Bedienung erwerben, quasi echtes „Learning-by-doing“ in kürzester Zeit.
In der letztlich voll befüllten Fassung werden bei Futterplatz.de 80 Roboter die Warenbewegungen durchführen und im Ausliefermodus bis zu 5 Picks pro Station und Minute ermöglichen. Die angegebene Pickleistung bezieht sich immer auf die Präsentation einzelner Warenträger. Wenn mehrere Artikel von einem Warenträger entnommen werden können, erhöht sich die Pickleistung dementsprechend signifikant.
Bereits mit dem aktuellen Füllungsgrad lassen sich die Abläufe gut erkennen: Der Picker sieht auf seinem Monitor die aktuelle Packliste. Gleich mehrere Roboter fahren schon zuvor die Wegstrecke zu den Liften und werden auf der richtigen Ebene abgesetzt. Anschließend navigieren sie selbstständig zur Position der jeweiligen Warenträger und docken sich daran an.
Mit dem Warenträger steuern sie auf ihrer Fahrbahn den Weg zurück zum Lift an und reihen sich an der zugewiesenen Ausgabestelle in Hüfthöhe ein. Durch die Tatsache, dass immer mehrere Picklisten vom System synchron bearbeitet werden, entsteht ein ununterbrochener Ware-zu-Mensch-Fluss.
Die Ware muss nur noch entnommen, gescannt und anschließend verpackt werden. Bei dem Scanvorgang wird der Artikel natürlich auf seine Richtigkeit überprüft und dann vom Lagerwirtschaftsprogramm ausgebucht.
Mit dieser Info weiß das System, welche Lagerposition aktuell frei ist und lässt den Roboter den Warenträger zur Abstellposition zurückund den nächsten Auftrag bringen. Bei der Wiedereinlagerung von Rücksendungen funktioniert die Verfahrensweise analog und erspart auch hier zeitaufwendiges Suchen von freien Lagerplätzen.
Wohin er fahren muss, welche Strecke, an welche Lagerposition und zu welcher Kommissionierstation „weiß“ und kontrolliert der Roboter durch die fortlaufend unter ihm gelesenen Codes sowie mit fortgeschrittenen Navigations- und Koordinierungsalgorithmen. Auch das Aufladen ihrer langanhaltenden Energiereserven übernehmen die Roboter im laufenden Betrieb bei Bedarf an fest installierten Ladeorten autonom und melden sich direkt wieder zum Dienst.
Dadurch, dass mehrere Roboter ständig im Einsatz sind, wird ein regelmäßiger Warenstrom erreicht, der schnell und sicher funktioniert und Mitarbeiter weitgehend unterstützt bzw. entlastet. Bei Futterplatz.de haben die Warenträger jeweils nur ein Fach und benötigen so eigentlich keine Kommissionierhilfe durch Pick-by-Light. Allerdings werden schwere und unhandliche Futtersäcke auf einer tieferliegenden Ebene angeliefert, um ein möglichst ergonomisches Arbeiten zu ermöglichen. Damit hier keine Verwirrung entsteht, zeigt das Pick-by-Light System lediglich, auf welcher Ebene gerade die zu entnehmende Ware durch die Roboter angeliefert wird.
Gute Perspektiven
Zur Freude von Futterplatz.de-Betriebsleiter Julius Schmidt lassen sich schon jetzt im teilgefüllten Zustand weitere Vorteile und ein immenser Gewinn an Flexibilität erkennen. Jede Kommissionierstation kann zum Ein- und Auslagern der Ware verwendet werden, so dass Personal und Einsatzzeiten den anstehenden Aufgaben besser zugeordnet werden können und auf Mitarbeiterwünsche leichter umsetzbar sind. Zudem ermöglicht STOROJET eine permanente Inventur, was bislang einen 2-tägigen „Liefer-Stopp“ sowie den Einsatz von 30 Personen erforderte.
Zum einen bestand bei den Mitarbeitern von Futterplatz.de anfänglich eine gewisse Reserviertheit der neuen Technologie gegenüber. Da gab es Neues zu lernen und eine Sorge um den Arbeitsplatz, die sich jedoch als unbegründet erwies, weil STOROJET das Wachstum in einem Maße unterstützt, dass künftig sogar weitere Mitarbeiter eingestellt werden sollen.
Zum anderen stand betriebswirtschaftlich die Frage im Raum, ob sich die Eigenentwicklung investitionsmäßig letztlich rechnet. Denn abgesehen von den Vorteilen eine solch passende Neuerung im Unternehmensverbund realisieren zu können, sollte es nicht teurer werden als die am Markt verfügbaren Alternativlösungen. Nach Aussage des Unternehmens lag die Investitionssumme bei rund € 730.000, während die Alternativen jeweils oberhalb der € 1 Mio. begannen.
Die zukunftsweisende Entwicklung von STOROJET enthält also nicht nur die für den Mittelstand so wichtige mehrdimensionale Flexibilität, sondern ermöglicht dies auch zum günstigen Preis!
Fazit
Abschließend meint Betriebsleiter Schmidt: „Nach kurzer Anlaufphase macht es richtig Spaß, mit STOROJET zu arbeiten! Bereits nach kürzester Zeit zeigte sich für die ausgewählten Produkte zur Einlagerung, im Vergleich zur Handkommissionierung, eine generelle Effizienzsteigerung von knapp 68%. Wir entlasten die Mitarbeiter von den mehr als sportlichen Kilometerleistungen am Tag. Und auch das Heben größerer Lasten werden wir in Kürze noch durch Saugnapfheber an den STOROJET-Kommissionierplätzen erleichtern. So ergeben sich zusätzlich Vorteile beim Arbeitsschutz und für die Gesundheit der Mitarbeiter. In Kombination mit der einfachen Skalierbarkeit haben wir so einen wichtigen Schritt in Richtung Zukunft gemacht. Unser STOROJET kann von Interessenten gern besichtigt werden, bestimmt bietet es auch anderen Mittelständlern optimale Lösungen für ihr Lager“.
Quelle: www.storojet.com
Schlagwörter: E-Commerce