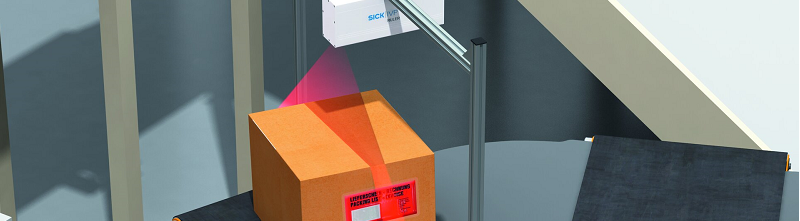
100 Orte der Industrie 4.0 in Baden-Württemberg: SICK gewinnt mit zwei Lösungen.
Im Rahmen des Wettbewerbs „100 Orte der Industrie 4.0 in Baden-Württemberg“ des Netzwerks Allianz Industrie 4.0 wurden sowohl das „Body Positioning System BPS5400“ als auch die auf Deep Learning Algorithmen basierende Lösung „Single Item Verification“ von SICK als Industrie 4.0 Lösung ausgezeichnet. Übergeben wurde der Preis von der Staatssekretärin im Ministerium für Wirtschaft, Arbeit und Wohnungsbau des Landes Baden-Württemberg, Katrin Schütz, im neuen Schloss in Stuttgart.
Zum Wettbewerb „100 Orte der Industrie 4.0 in Baden-Württemberg“ hatte der Sensorhersteller SICK zwei Lösungen eingereicht – sowohl das Body Positioning System BPS5400 (BPS) für die Automobilfertigung als auch die auf Deep Learning Algorithmen basierende Lösung „Single Item Verification“ für den Einsatz im Paketversand haben gewonnen. „Industrie 4.0 ist einfach, denn wir arbeiten mit vorhandenen Daten, die uns Sensoren liefern. Damit lassen sich Herausforderungen lösen, die zuvor unlösbar schienen“, erklärt Bernhard Müller, Senior Vice President Industry 4.0 bei der SICK AG. „Unsere beiden Gewinner-Lösungen sind nur beispielhaft für das, was heute schon im Bereich Industrie 4.0 möglich ist“, ergänzt Müller.
Sensor Intelligenz im Body Positioning System BPS5400
SICK ist mit über 40.000 Produkten einer der größten Sensorhersteller weltweit. Der Fokus liegt bereits seit 2014 darauf, Intelligenz und Sensoren zu „Sensorintelligenz.“ zu verknüpfen. Das Ziel: Daten generieren und nutzbar machen. Das war auch der Ansatz, mit dem das BPS entwickelt wurde.
Konventionell wird im Automobilbau die Karosserie mit Hilfe von aufwändigen mechanischen Positionier- und Spannlösungen in den Fertigungszellen zentriert. Die Fahrzeugkarosserien werden hierfür in jeder Zelle auf Aufnahmedorne bzw. –stifte abgesenkt und verspannt. Mit dem kontaktlosen BPS, bestehend aus vier Sensoreinheiten, wird die Position von Fahrzeugkarosserien in der Automobilproduktion hochpräzise ermittelt. Dies ermöglicht eine hochflexible, adaptive Roboterführung verschiedener Applikationen und eliminiert gleichzeitig die Mechanik als größten limitierenden Faktor in der Automobilproduktion. Insbesondere für die Multiplattform- und Multimodellstrategie der Automobilhersteller im Zuge der Elektrifizierung von Fahrzeugen eröffnet das System neue Möglichkeiten. Mit erweiterten Funktionen haben Anwender die Möglichkeit den Produktionsprozess transparent zu erfassen und zu dokumentieren. Außerdem werden Analysen von Big Data für die Ableitung von Trends zur Prozessregelung, Einbindung von Cloud Computing und Remote Access ermöglicht. Die Analysen helfen, die Qualität der Fahrzeugproduktion zu verbessern und die Produktivität zu erhöhen.
Deep Learning in der Vereinzelung von Paketen
Die Veränderung der Warenströme insbesondere durch den Online-Handel führen zu steigenden Pakettransporten vom Hersteller bis zu den Endkunden. Die logistische Kette und die Vielzahl der Warensendungen sind eine wachsende Herausforderung, bei der insbesondere Versandfehler vermieden werden sollen. Im aktuellen technischen Stand ist die automatische Vereinzelung, insbesondere in Verbindung mit automatischer Entladung nicht vollkommen und muss teils manuell geprüft werden. Mit der K.I.-Lösung „Single Item Verification“ – basierend auf einem trainierten, künstlichen, neuronalen Netz – ist es möglich, die Qualität der Vereinzelung zu verifizieren. Erst dadurch ist die vollautomatische Entladung realisierbar und damit ein Wegbereiter für die Weiterentwicklung des vollautomatischen Sortierprozesses.
Quelle: www.sick.de
Foto „head“: Mit der K.I.-Lösung „Single Item Verification“ ist es möglich, die Qualität der Vereinzelung zu verifizieren.
Schlagwörter: Sick