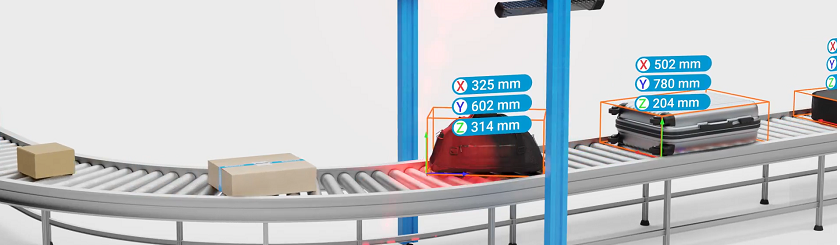
How to speed up logistics operations with novel 3D vision technology
The logistics and e-commerce sectors are dependent on modern technologies and automation to keep pace with the growing demand for fast order fulfillment and delivery. Intelligent, vision-guided robots can work faster and more efficiently than human workers. In many cases, they can inspect products with greater accuracy and identify errors with higher reliability. As a result, they produce less waste, which leads to significant cost savings.
3D vision helps to navigate a robot in 3D space, recognize objects, inspect them, pick them, or perform some other action such as sorting based on predefined criteria. Traditional 3D vision technologies can only recognize objects that do not move – otherwise, the 3D image is degraded by motion artifacts. Though Time-of-Flight and active stereo methods can create 3D point clouds in fast motion, the quality is not perfect. The 3D output has generally low resolution with high noise levels.
How to solve this dilemma if you need to handle objects in fast motion with perfect accuracy and reliability?
A completely new approach to 3D sensing was developed by Photoneo, a Slovakia-based company that develops machine vision and smart automation solutions. Their novel technology of Parallel Structured Light, which is implemented in the 3D camera MotionCam-3D, enables the capture of scenes in motion and their reconstruction in the form of a 3D point cloud in submillimeter accuracy and high resolution.
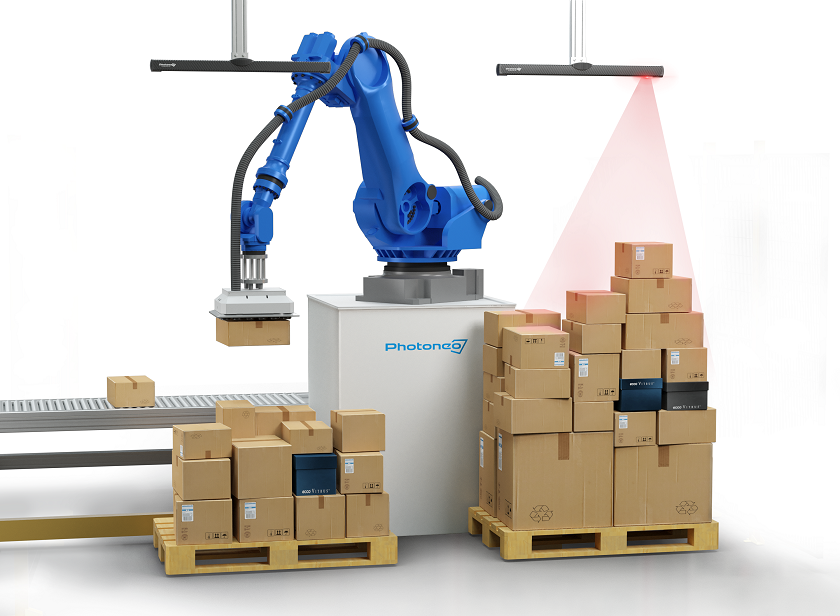
Automated palletization / depalletization
What does this mean in practice?
You can automate all kinds of logistics tasks and achieve high speed of operations without interrupting the workflow, thus increasing productivity, efficiency, and throughput.
Imagine a robot navigated by a 3D vision system that needs to pick items from a moving conveyor belt. Typically, there must be no movement during scan acquisition, which means that either the conveyor belt needs to be stopped to scan each item (in case the 3D scanner is attached in a fixed manner somewhere above the conveyor) or the robot itself needs to stop moving (if the scanner is attached directly to the robotic arm). This prolongs cycle times and decreases throughput.
MotionCam-3D enables you to scan moving items continuously and without interruption. When each parcel gets within reach of the robot, the camera scans it and sends its 3D coordinates to the robot so that it can navigate to it and pick it. The robot can even sort the parcels and drop them in the right container based on the delivery company or other criteria.
If you need to pick items from shelves, you can maximize the operation speed by using a mobile robot with MotionCam-3D attached to its arm. The camera scans the shelf while the robotic arm approaches the items. Based on the 3D data, the system localizes the item to be picked and navigates the robot to grab it. All this happens during constant motion, which saves time and increases efficiency.
The possibility to scan in motion can also boost the palletization and depalletization processes and increase accuracy and speed of dimensioning applications. Automated measurement and precise calculation of objects’ dimensions is frequently used in package handling or pallet dimensioning to calculate transportation costs or how much space the boxes will take up in a transportation container. If this is done in motion and without interrupting the workflow, you will get much higher throughput and efficiency than with conventional 3D sensing technologies.
3D scanning in motion can also increase the speed and accuracy of counting or inspecting parcels that are moving on a conveyor belt. The large scanning volume of MotionCam-3D enables you to scan even very large objects measuring up to 1,5 x 1,5 x 1,5 m.
MotionCam-3D is also available in a color version so now you can create real-time, colorful 3D point clouds in high quality and in motion. This feature is very handy if you need to inspect or sort items based not only on their 3D geometry but also color features.
The technology enables you to capture objects moving up to 144 km/h, offering a resolution of 0.9 Mpx and accuracy of 300 – 1,250 µm, depending on the model. However, you can also use it for scanning static scenes and get a resolution of 2 Mpx and accuracy of up to 150 – 900 μm.
Quelle: www.photoneo.com
Schlagwörter: Photoneo